Recycling Strategies
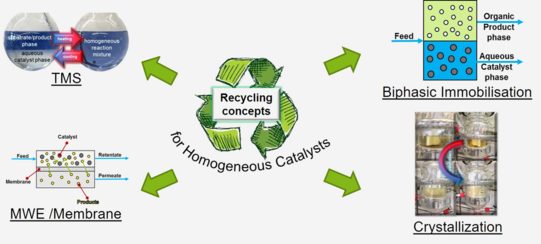
Thermomorphic Multiphase Systems (TMS)
A strategy for separating catalyst and product as well as overcoming mass transport limitations is the use of thermomorphic multicomponent solvent systems (TMS) which have some decisive advantages over other process variants:
- Thermomorphic phase behaviour: Reaction control takes place without mass transport limitations between catalyst and substrate
- The catalyst and product are separated by simple decantation after the reaction
- Cheap and commercially available solvents can be used without additional surfactants, etc.
The technic of the TMS system uses the temperature dependence of the mixing gap between two solvents: a polar, catalyst-containing solvent and a nonpolar substrate phase. This system is two-phase at room temperature and forms a single-phase system when heated. This minimizes the mass transport limitation.
Angew. Chem. Int. 2016, Int. 55, 2924-2928 DOI: 10.1002/anie.201510738
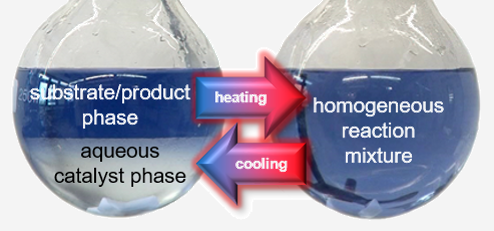
Biphasic Immobilisation
The core of the process is the separation of the catalyst from the reaction products by generating two practically immiscible liquid phases which can be separated by simple phase separation. The phases consist of an aqueous phase in which the catalyst is dissolved and an organic phase formed from the reaction products n- and iso-Butanal. This concept of two-phase immobilization is transferred to other reactions in our working group in order to separate the catalyst from the product.
Appl.Cat. A Gen. 2017, 539, 90-96, DOI: 10.1016/j.apcata.2017.03.037.
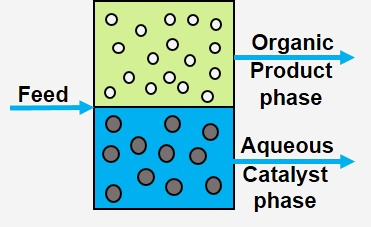
MWE / Membrane
The basic principle of membrane separation is quite simple (see figure): A feed containing substrates, products and the catalyst flows over a membrane. Ideally, only the small products can pass through the membrane into the permeate stream, the rest remains in the retentate, which is returned to the reactor. Membrane separation processes operate without heating and therefore use less energy than conventional thermal separation processes such as distillation or crystallization.
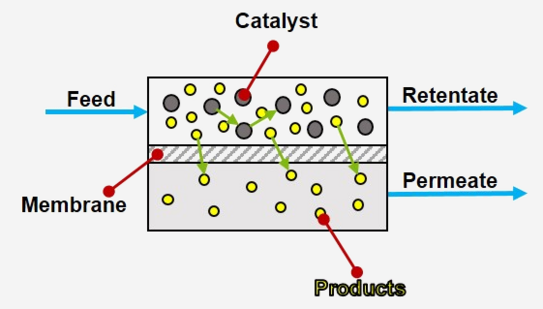
Advantages:
- No restrictions due to phase equilibria and thermal treatment
- Recycling of the catalyst is possible without thermal load
- Low energy consumption and simple numbering-up of the membranes to the desired process specification
At our chair we work with different types of membranes such as ceramic or polymer membranes in different reactor structures to investigate their behaviour.
Chem. Eng. Process 2016, 99, 124 –131, DOI: 10.1016/j.cep.2015.07.019
Crystallization
One catalyst recycling strategy is product crystallization for the selective and easy separation of the catalyst and the product. During product crystallization, the reaction solution is slowly cooled down in temperature intervals by means of a crystallizer and a cryostat. By crystallizing the product, it is possible to filter off the reaction solution and recover the product. This process is a gentle process for the product and for the catalyst and the ligands used.
ChemCatChem 2017, 9 (23), 4319-4323, DOI: 10.1002/cctc.201700965
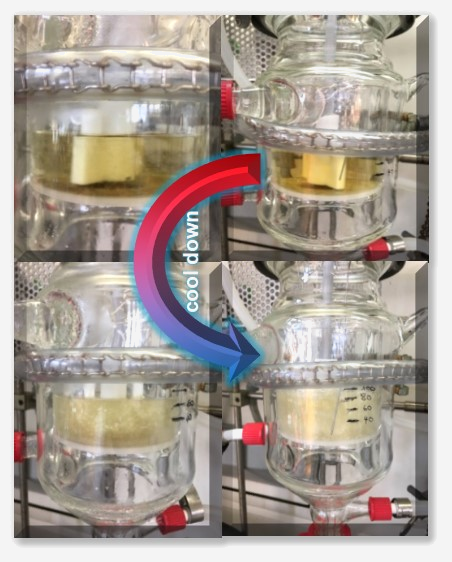