Process Development & Online Analytics
CSTR + Mixer settler + Distillation
The challenging task of rhodium catalyzed hydroformylation with higher olefins is the efficient combination of the reaction and separation step for catalyst recovery and recycling. One promising concept is the use of organic solvent systems, which use a strong polar organic phase for the catalyst and allow a liquid/liquid-separation of product and catalyst after the reaction step. In this work, the hydroformylation reaction with 1-dodecene is presented in discontinuous lab-scale investigations as well as continuously driven in a miniplant. The hydroformylation reaction is carried out in a two- component solvent system.
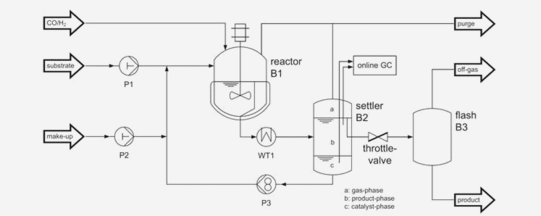
Dreimann, J. et al. "Rhodium catalyzed hydroformylation of 1-dodecene using an advanced solvent system: Towards highly efficient catalyst recycling". Chem. Eng. Process 2016, 99, 115 – 123. DOI: 10.1016/j.cep.2015.06.014
CSTR + membrane filtration
Homogeneous transition metal catalysts allow highly selective conversion of reactants at mild reaction conditions. Main drawback of this catalytic method is a difficult recovery of the catalyst, dissolved in the reaction phase. One recovery method is the decrease of the temperature in the reaction phase in order to generate two phases in which the product and the catalyst show different solubilities. This is known as thermomorphic multicomponent solvent (TMS) system. Another method to separate the catalyst directly from the reaction phase is the application of the organic solvent nanofiltration (OSN). For an efficient catalyst separation a combination of both concepts might be necessary.
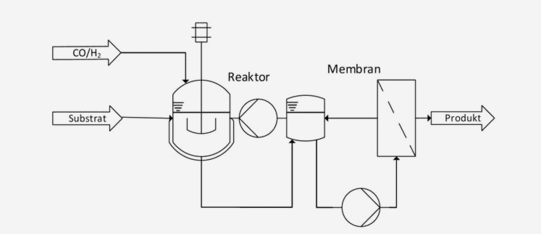
Dreimann, J. et al. “Highly integrated reactor–separator systems for the recycling of homogeneous catalysts”, Chem. Eng. Process. 2016, 99, 124 –131. DOI: 10.1016/j.cep.2015.07.019
CSTR + ex situ extraction
Hydroformylation of alkenes for the production of aldehydes is one of the most important homogeneously catalyzed reactions on an industrial scale. Mostly, these processes are based on expensive rhodium as the catalyst metal. In this contribution, we present for the first time the successful application of ruthenium as a cheaper alternative metal in a continuously operated miniplant. In the reaction of 1-octene, ex situ ex-traction of the oxo-products is conducted using the nonpolar solvent iso-octane, while the catalyst is retained in a polar DMF phase.
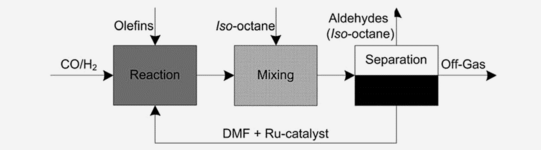
Kämper, A. et al. "Ruthenium-catalyzed hydroformylation: from laboratory to continuous miniplant scale", Catal. Sci. Technol. 2016, 6, 8072–807. DOI: 10.1039/C6CY01374K
CSTR catalyst immobilization
This paper presents the homogeneous catalyzed hydrogenation of carbon dioxide to N,N-dimethylformamide (DMF) with an in-situ generated ruthenium catalyst based on RuCl3 × H2O and the phosphine ligand 2,2-bis(diphenylphosphinomethyl)-1,1-biphenyl (BISBI). Investigations showed that the complex formation of an active species requires the presence of an amine. The catalyst was recycled by immobilization in a nonpolar alcoholic solvent while the formed product was extracted in-situ into the aqueous phase
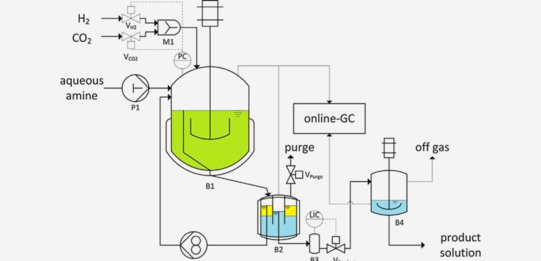
Kuhlmann, R. et al. "Process development of the continuously operated synthesis of N,N-dimethylformamide based on carbon dioxide", J. CO₂ Util. 2017, 22, 184–190, DOI: 10.1016/j.jcou.2017.10.002
Jetloop + Biphasic Immobilization
To overcome the challenges of the increasing global energy and feedstock prices intensified process equipment is one way to develop new efficient production pathways for the chemical industry. In this article the authors convey a thorough overview about the jet loop reactor technique. Ensuing an introduction the operation principle of the reactor type is elucidated. Information available in the literature regarding dimensioning and the physical description is summarized in the following to give an outline of constructional possibilities. To underline the main advantages of the set up the macro and micro mixing properties are discussed in detail and exemplary data is presented. Applied chemical and biochemical reactions are reviewed, with particular focus on the enhancement of catalytic reactions subdivided in homogenously, heterogeneously and biocatalyzed conversions.
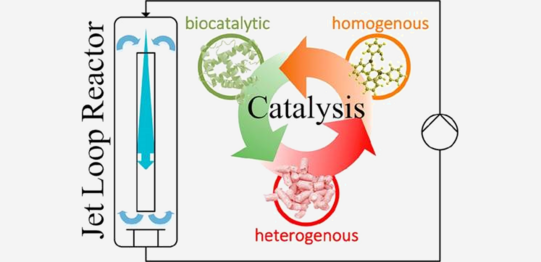
Warmeling, H. et al. "Jet loop reactors as a versatile reactor set up - Intensifying catalytic reactions: A review" Chem. Eng. Sci. 2016, 149, 229-248, DOI: 10.1016/j.ces.2016.04.032
Jetloop + Membrane
The aim of this research is to design a continuous jet-loop reactor with coupled nanofiltration combining the experience from research on nanofiltration separation and re-use of homogeneous catalysts, jet-loop reactor technology and the combination of membrane filtration and jet-loop technology. Cyclooctene was chosen as a model substrate for an internal alkene, for which C C double bond isomerisation does not lead to regioisomer products. Thus, the rate equation for the hydroformylation of cyclooctene for the Rh bulky phosphite-modified catalyst had to be derived, based on a plausible reaction mechanism. Furthermore, the kinetic parameters in the rate equation had to be estimated. Together, this will form the basis for conducting experiments in the new setup.
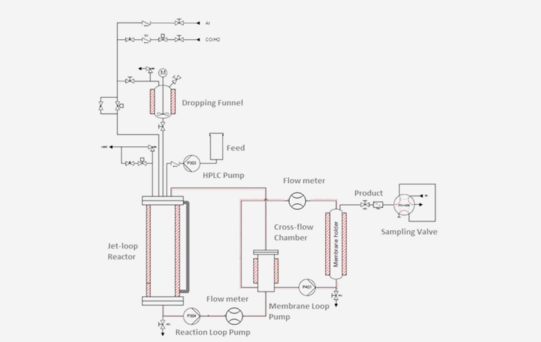
Güven, S. et al. "Kinetic Explanation for the Temperature Dependence of the Regioselectivity in the Hydroformylation of Neohexene" ChemCatChem 2014, 6, 603-610, DOI: 10.1002/cctc.201300818
TMS in a Taylor–Couette reactor (TCR)
In order to design an innovative continuous process for the conversion of the renewable beta-myrcene, three methodical steps are shown in this paper to find a setup for the demanding homogeneously catalyzed hydroamination. First step is the theoretical and practical design of a suitable thermomorphic multicomponent solvent (TMS)-systems for recycling the catalyst system. A Taylor–Couette reactor (TCR) was developed and modified for the application in homogeneous transition metal catalysis. The reactor was integrated in a miniplant setup and a continuous recycling of the catalyst phase as well as an efficient synthesis of the desired terpenyl amines is achieved in 3 complete cycles. The results show that the TCR is suitable for the hydroamination and generates high conversion and yields (XMyr = 82%, YHA = 80%). Recycling experiments were conducted successfully in the miniplant setup to show the long-term operation in a period of 24 h.
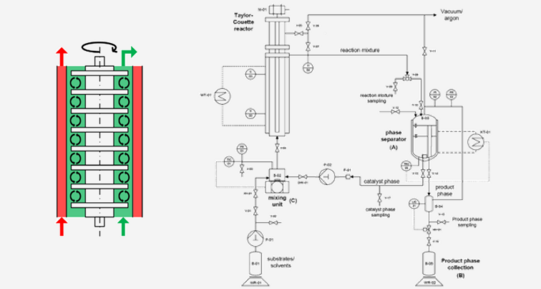
Färber, T. et al. "Homogeneously catalyzed hydroamination in a Taylor–Couette reactor using a thermormorphic multicomponent solvent system" Chem. Eng. Res. Des. 2016, 112, 263-273, DOI: 10.1016/j.cherd.2016.06.022